Chlorination is one of the most widely used methods of disinfection in drinking water treatment. Proper chlorination ensures the safety and quality of drinking water. To enhance the consistency and safety of chlorination practices, the World Health Organization (WHO) recommends water treatment plants (WTPs) develop comprehensive standard operating procedures (SOPs).
SOPs serve as detailed instructions for staff to perform tasks consistently and safely. For chlorination, SOPs provide clear guidance on how to prepare, apply, and monitor chlorine levels, minimizing risks and errors. By having documented procedures, organizations can ensure that every team member, regardless of experience, can follow the same protocols, enhancing overall operational efficiency and safety. Operations managers who do not have established SOPs or who wish to update or revise existing procedures can use this article, which summarizes select aspects of WHO’s structured approach.
Key Components Of Effective SOPs
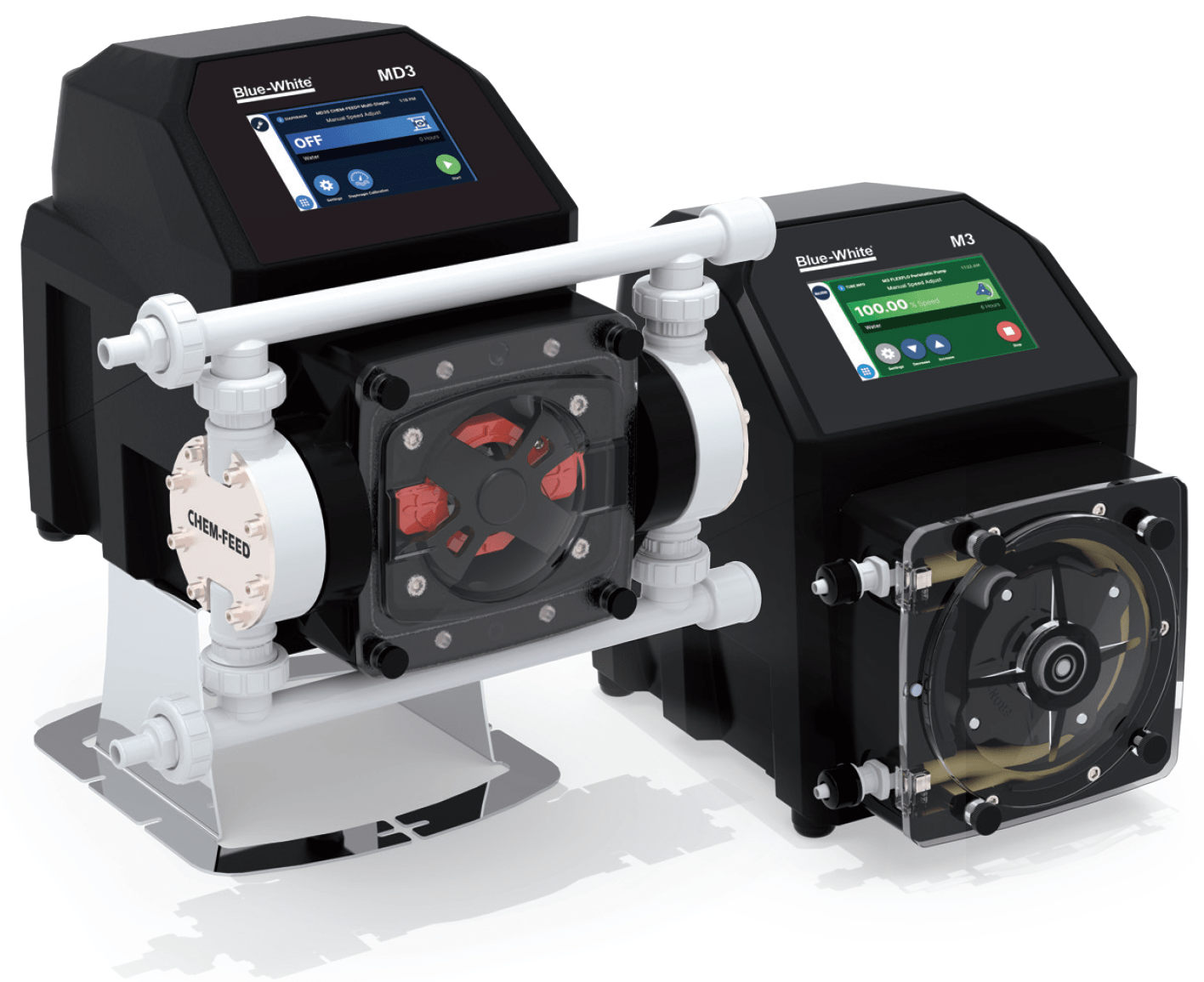
For the most effective chlorination SOPs, WHO recommends they contain four key elements:
- Clarity and conciseness. SOPs should be straightforward and avoid unnecessary jargon or overly complex instructions. In order to ensure adherence, each procedure should be easy to understand for all trained personnel. For example, using simple language and limiting the amount of text per step can help ensure that even less experienced staff can follow the instructions accurately.
- Visual aids. WHO suggests incorporating visual elements, such as diagrams or photographs, which can significantly enhance the usability of SOPs. Visuals help staff of varying levels of literacy and English language fluency to comprehend key steps and ensure that processes are followed accurately. For instance, a picture showing the correct mixing apparatus or protective personal equipment (PPE) can serve as a quick reference.
- Targeted information. Each SOP should focus specifically on the chlorination task at hand. As an example, an SOP for calculating the weight of chlorine powder needed to prepare a liquid batch, include:
- Required personal protective equipment (PPE).
- Type of chlorine powder to be used (e.g., bleaching powder or high-test hypochlorite).
- Desired solution strength and volume.
- Step-by-step calculations for determining the appropriate weight of chlorine powder.
- Safety Protocols. Safety is a top consideration in any chlorination procedure. Each SOP must include crucial safety information, such as the required PPE, safe handling practices for chlorine and its derivatives, and emergency procedures in case of chlorine exposure or spillage. For instance, the SOP for preparing a batch of liquid sodium hypochlorite should specify the receptacles to use and the necessary mixing equipment, while also highlighting the importance of following proper safety measures throughout the process.
Critical Chlorine SOPs
Every disinfection SOP should include certain key tasks, such as:
- Chlorine dose calculation. The document should explain the methodology for determining the appropriate dose based on flow rates, the types of adjustments that may be needed during operation, and protocols for increased monitoring.
- Operation and maintenance of chlorine dose pumps. Chemical metering pumps are the most common way to administer chlorine in water treatment. SOPs should include details on how to operate and maintain this equipment. Specific steps should follow manufacturer recommendations, but must include any required PPE required, how to adjust the dose pump set-point, maintenance and calibration basics, and guidance on troubleshooting common metering pump faults or failures.
- Monitoring chlorine levels. Effective chlorination requires continuous monitoring. As such, SOPs should outline procedures for collecting water samples for chlorine testing, interpreting results, and taking corrective action when necessary. They should also cover when and how to schedule checks. If the plant uses online monitoring systems, their use, calibration, and maintenance must also be documented.
Training And Competency Assessment
Once a water treatment plant has developed and published its SOPs, management must train staff on them. The WHO recommends regular training sessions, alongside competency assessments, to ensure that staff members are not only familiar with the procedures but also understand their importance in maintaining water quality and safety. This training should be ongoing and incorporate feedback from staff to refine procedures as needed.
Developing SOPs for chlorination is essential to ensuring the safety and effectiveness of water treatment processes. By prioritizing clarity, conciseness, and safety, WTPs can equip their staff with the tools necessary for consistent and reliable chlorination practices. Regular training and monitoring will further enhance operational integrity, ensuring that water remains safe for public consumption. Ultimately, well-crafted SOPs are not just documents; they are foundational to the effective management of water quality.
Blue-White Industries manufactures full lines of both Diaphragm type and Peristaltic type chlorine dosing pumps, as well as complete metering systems, often called Skid Systems.
Peristaltic Metering Pumps, which are also referred to as Roller Pumps, Hose Pumps or Tube Pumps, are a type of positive displacement pump. Although they may operate today in a similar manner as they traditionally have, advancements in technology, enhanced design features, and highly functioning materials have significantly improved the capabilities and operation of peristaltic pumps.
Peristaltic pumps are extremely effective when dosing fluids that off-gas, such as chlorine, because they are not affected by air bubbles… bubbles simply pass through the tube. There is no vapor lock and no loss of prime.
Multi Diaphragm Metering Pumps utilize two diaphragms connected through a central shaft. The shaft pulls one diaphragm to create suction while simultaneously pushing the other diaphragm to discharge liquid. The push pull combination creates a smooth flow that allows the pump to run at high speeds without water hammering. In addition, the dual pushpull action means the pump is resistant to vapor lock, allowing it to handle off gassing chemicals.
When choosing equipment for accurately, and repeatably, dosing chlorine, we hope you’ll consider contacting Blue-White Industries.
Written by:
Blue-White® Industries
714-893-8529