Cooling towers and chillers are an increasingly common technology employed in a range of industries, from power generation to manufacturing, as well as for HVAC systems in hospitals, schools, large commercial buildings, and more. These systems use water to help dissipate heat and ensure that equipment and the targeted environment remain at optimal temperatures.
It must be considered that water used from any source, including tap water, will contain impurities or have properties that can be detrimental to the cooling system. Impurities are compounded by exposure to the ambient air and will accumulate over time. Left unchecked, these conditions can cause damage to cooling systems they serve to protect and jeopardize the safety of workers and nearby populations. In-house chemical treatment can be the go-to answer. For example, chemical metering pumps are a highly effective and affordable option in most applications. But the wrong combination of pump and chemical can lead to both short-term and long-term problems that may increase costs, damage equipment, and more.
Challenges Faced with Cooling Systems
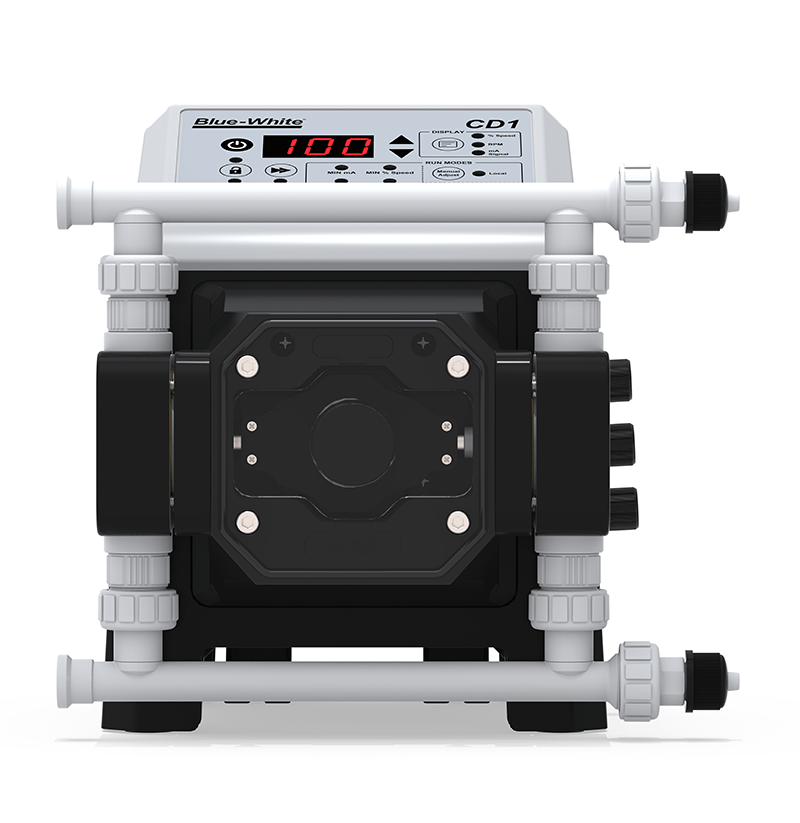
Biological growth. The application of water in warm environments can create a breeding ground for bacteria, mold, and viruses. This leads to fouling of cooling surfaces and the potential breeding of deadly Legionella bacteria. As such, many cooling towers require the application of biocides to keep this at bay. Bromine, chlorine, and peracetic acid (PAA) are the most commonly used disinfectants in cooling towers. However, these chemicals may present their own set of challenges, including, offgassing, corrosion, and crystallization.
Corrosion. The presence of dissimilar metals, low pH, or excess oxygen in water can all cause corrosion. Corrosion will impact the cooling tower’s efficiency and may also increase downtime due to increased maintenance requirements. While corrosion inhibitors are typically easy to meter, they must be dosed precisely; not enough chemical will fail to mitigate corrosion, but too much may cause alkalinity or scaling.
Foaming. Agitation, dissolved gases, and even microbial activity can all result in foaming, which reduces heat-transfer efficiency. Foaming may also increase scaling or corrosion by trapping contaminants in air bubbles, preventing other chemicals from reaching them. Anti-foaming agents are typically hydrophobic, meaning they will not naturally mix. As such, they must be metered precisely to ensure even distribution.
Scaling. Highly alkali, hard water, can cause scaling on equipment which can require continuous cleaning. Like corrosion inhibitors, anti-scaling chemicals are often proprietary and can include a combination of chemical substances designed to address different types of scaling. As with other chemicals in use, precise dosing of these chemicals is critical in order to ensure they will sufficiently reduce scaling without lowering pH and potentially causing corrosion.
How the Correct Chemical Feed Pump Will Simplify the Process
Chemical dosing / metering seems like a simple process of purchasing a chemical feed pump and turning it on and off as needed. While it’s true that chemical metering doesn’t have to be complicated, it is still critical to ensure that the right pump is purchased for the application. Here are some key factors to consider that can save time and expense, while also ensuring the process is as simple as possible.
Correct Chemical Feed Pump Size. The flow capability of the metering pump must easily meet the requirements for dosing the chemical being injected. A pump that is too small will run at or near maximum speeds for long periods of time, which can overtax the motor and lead to excess maintenance or worse may cause the pump to fail prematurely. Conversely, an oversized pump will run at the lowest speeds, which can make accurate dosing difficult.
Metering Pump Technology. There are many types of pumps on the market, although the two most common are diaphragm pumps and peristaltic pumps. Each has its benefits particularly when considering the chemicals being dosed. For example, typically diaphragm pumps struggle with chemicals that off-gas, however, some are now equipped with an automatic degassing valve that can help eliminate problems with vapor locking. In addition, the newer technology of multi-diaphragm pumps (Figure 1) which feature a dual diaphragm design, allows for fluid to be pumped at smooth, near continuous flow, mimicking the best traits of peristaltic pumps and preventing those two common problems often associated with diaphragm pumps, vapor lock and loss of prime.
Material compatibility. Just as the chemical being metered can influence the pump technology, it may also influence the material being used for tubes, hoses, diaphragms, pump heads and other pump components. It is critical to work with vendors, and research data to ensure material compatibility.
Dosing accuracy. Proper water treatment in cooling systems requires that the chemicals in use are being accurately dosed.. For example, too much disinfectant can cause corrosion. However, lowering the pH to reduce scaling can make disinfectant less effective. There are a number of features and technology that can ensure pumps dose chemical accurately, including synchronizing the pumps with flow meters or other sensors, automatic timers, and more.
The Cost Factor
While metering pumps are not the most costly component associated with cooling towers or chillers, it is important not to presume that the smallest and least expensive pump is the best way to keep costs down. Lower-quality pumps may actually cost more in the long run, as they are often less accurate, require more frequent maintenance, and don’t last as long as higher quality products. The pump itself isn’t the only source of potential costs; a less effective chemical metering system is going to provide less effective chemical treatment, which in turn can make the cooling tower less efficient, increase associated maintenance, and increase exposure to safety violations, which can be far more costly than any given pump. Therefore, it is critical to work with vendors to determine the best possible solution.
Written by:
Blue-White® Industries
714-893-8529